共计 826 个字符,预计需要花费 3 分钟才能阅读完成。
01
CPK与合格率的关系
Cpk衡量的是过程输出满足规格要求的能力,计算公式为:
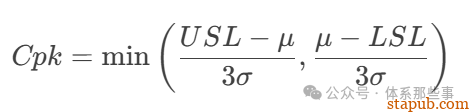
其中:
- USL/LSL:规格上下限
- μ:过程均值
- σ:过程标准差
当Cpk=1.33时,意味着过程均值与最近的规格限之间有 4σ 的距离(因为 1.33×3σ≈4σ1.33×3σ≈4σ)。根据正态分布
- 理论合格率:99.994%(仅0.006%的不合格率,即6ppm)。
- 实际缓冲:即使过程均值发生小幅偏移(如±1.5σ),合格率仍能保持在99.38%(6210ppm),满足大多数企业要求。
02
行业中的关键因素
1、预防变异和偏移
生产过程中难免存在均值偏移(如设备磨损、原料波动等)。Cpk≥1.33为过程提供了安全余量,即使均值偏移1.5σ(常见假设),仍能保证Cpk≥1.0,合格率可控。
6σ管理中,Cpk≥1.67(对应5σ水平)是理想目标,但1.33是许多行业的入门门槛。
2、降低质量成本
早期发现缺陷:高Cpk减少返工、报废和客户投诉的成本。
减少检验频次:过程稳定后可放宽检验,节省资源。
3、客户与行业标准
汽车行业(IATF 16949)、医疗器械(ISO13485)等行业强制要求Cpk≥1.33,否则供应商可能被淘汰。
客户合同条款:许多大客户将Cpk≥1.33写入采购协议。
03
不同CPK值的对比
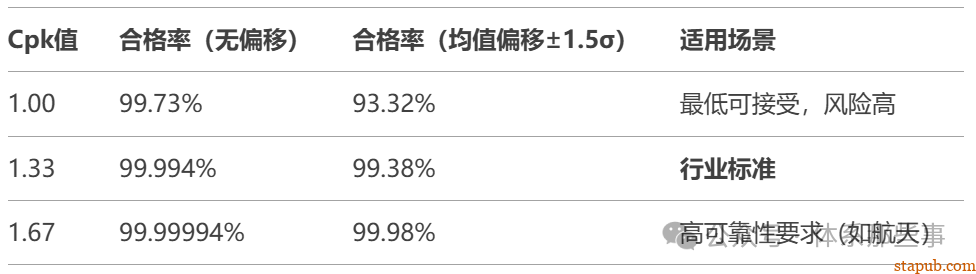
04
为什么不是更高(如Cpk≥1.67)?
1、成本平衡:
- 提升Cpk需更精密设备、更严格工艺,可能增加成本。
2、必要性:
- 1.33已能满足大多数工业品的质量需求,更高要求仅用于关键领域(如芯片、航空)。
- 动态监控:
- Cpk需定期验证,防止过程退化。
-
与Ppk区别:
- 初期小批量生产用Ppk(性能指数),长期稳定后用Cpk。
-
非正态数据:
-
若数据非正态分布,需转换或使用其他指标(如Pp/Ppk)。
-
正文完