共计 3658 个字符,预计需要花费 10 分钟才能阅读完成。
FMEA即 Failure Mode and Effect Analysis-失效模式及影响分析,是汽车行业产品设计及开发过程中常用的风险管理工具,其根本目的是实现稳健的产品及过程设计。一般来说FMEA有以下三类:
- PFMEA-Process FMEA,用于过程设计
- DFMEA-Design FMEA,用于产品设计
- CFMEA-Concept FMEA,用于概念设计
二、FMEA的发展历史
一般认为美国航空航天局NASA在其1960年代的阿波罗项目中首先开始应用FMEA,尔后福特汽车在1970年代将FMEA推广至汽车行业,目前几乎所有工业领域都在广泛使用FMEA。下图简要展示了FMEA发展历史。
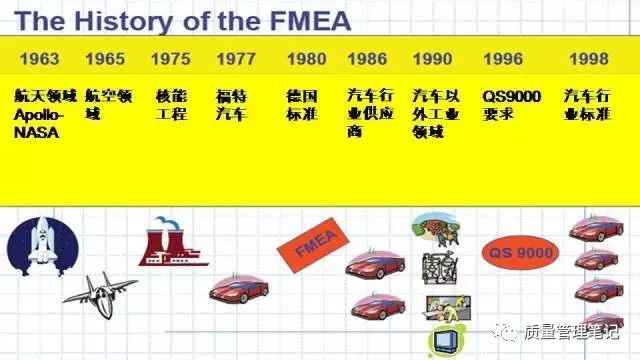
2)动态文件
PFMEA和Control plan一样,是一个动态文件(a living document),需要不断的完善更新,并始终展示最新修订日期及原始文件编制日期。
3)团队工作
PFMEA是一项团队工作,由一个人做出来的那不是PFMEA,而只是个形式。PFMEA开发的参与者包括核心团队(core team)及支持者( Supporter),其中核心团队一般是要参与到PFMEA的每个阶段的Stakeholders,一般要包括技术部门、制造部门、质量部门等;支持者supporter要包括领导者及其他部门,他们在需要时提供支持,如PFMEA最终要由负责技术的管理层参与审批。
PFMEA内容要达成团队共识,注意团队共识不是少数服从多数,也不是下级服从上级,而是在讨论过程中逐渐达成一致。
4)逻辑严密(Robust)
在开始讨论PFMEA之前,一般会先有PFD-Process Flow Diagram-过程流程图, 在PFMEA之后有过程控制计划 PCP-Process Control Plan;PFD、PFMEA、PCP三大文件的逻辑要保持一致,最基本的要求是三者的步骤编号要一一对应。(PFD确保失效分析不出现遗漏项,PCP明确PFMEA中所确定的控制措施,PCP中所列出的控制措施及反应计划应在相应的OIS中体现)
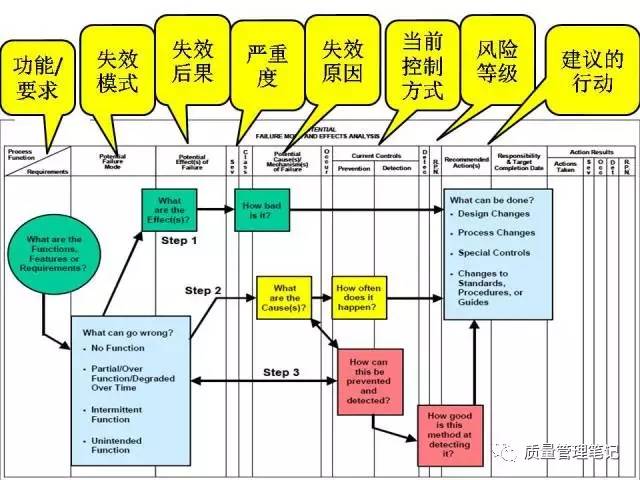
- 过程特性: 过程参数及过程要求,即加工条件和加工参数
- 产品特性:产品规范,如尺寸\性能
对于同一个Operation上有多个操作动作的(an operation for a multistation machine or sequential process in one piece of equipment), 不管是人工操作还是极其操作,需要细化到每一个操作,比如:
• Operation #20: Drill hole size Xmm, through depth
• Operation #20A: Weld part A to part B forming subassembly X
• Operation #20B: Attach subassembly X to assembly Y
PFMEA中明确功能要求非常关键,功能要求不明确,则失效模式会遗漏。 定义功能要求尤其要注意新工艺, 新技术, 新环境,以及以前出过问题的环节。
2)潜在失效模式
失效模式是针对特定Operation进行的, 对象包括过程特性和产品特性; 某失效模式可能会成为下游工序另一个失效模式的原因,也可能是上游工序某失效模式的结果。一般来料问题不列入失效模式分析,即一般假定来料是满足要求的(来料的变差可能需要考虑),除非历史记录显示该来料存在不可解决问题,需要在后续制造过程中予以关注。
失效模式的确定方法:功能丧失、功能过度/降低、间歇性功能、功能随时间的衰退、非预期功能。 失效模式分析要回顾DFMEA的功能要求,以及同类或类似产品的历史问题。
3)失效模式的后果(影响)
后果分析是要站在顾客的角度,即分析失效对顾客的影响。顾客包括内外部客户,及法律法规要求(如环保法):
• Operator safety
• Next user
• Downstream users
• Machines/equipment
• Vehicle operation
• Ultimate customer
• Compliance with government regulations
4)严重度
对于有多个不同失效模式的操作,严重度记录“影响最恶劣”的那一个;严重度只能通过变更产品或过程设计来降低;影响安全的失效模式严重度取9-10,严重度为1的可不进行分析。
5)潜在失效原因
此条的分析的是,当一个失效模式出现时,我们可以针对哪些环节作一些纠正或控制。一个失效模式可能对应多个失效原因,判断失效原因是否全部找到的方法是,问一个问题:如果纠正了这些原因后失效就100%消除了吗?有时候我们会难以判断多个原因中哪些是主因,这个时候我们可能会用到DOE试验设计。如失效原因最终没能找到,则应针对失效模式采取遏制措施(探测控制)。
失效原因的描述要具体,不能模棱两可,如“operator fails to install seal”是具体的可接受的,而“operator error” ,“machine malfunction”这种宽泛的描述则是不合格的。
6)特性分类
影响整车安全、产品功能、法律法规符合性、操作安全(operator safety)、顾客满意的特性(过程&产品)需要作识别。具体符号根据顾客及组织的流程要求确定。
7)发生度
发生度应针对失效原因分别确定,若无法分清某个失效原因对应的失效发生率,则按保守原则以失效模式的所有发生率来确定发生度。失效发生率包括:本过程步骤检验探测到的发生率、流到下游工序的发生率、流到直接客户的发生率以及在最终用户处所反馈的发生率。
8)当前控制方式
当前控制措施包括预防控制(error/mistake proofing or Statistical Process Control)和探测控制(post-process evaluation),“当前措施”应是在本过程或类似过程的中已落实的措施或已证明有效的措施。
预防控制优先于探测控制,因此首先要考虑预防控制。预防控制措施可以影响发生度但不能降低严重度;探测控制措施影响探测度,但不会影响严重度和发生度。预防和探测控制措施都可以针对失效原因和/或失效模式。
当失效原因与设计有关时,意味着需要在过程中采取预防(防错)或探测(探错)等措施弥补设计暂时无法克服的缺陷,对于不能避免/预防的问题,考虑更改设计。
注意:所确定的控制措施必须能验证其有效性,“加强培训”不是真正的预防控制措施,它的有效性无法得到验证,PFMEA中应杜绝将“加强培训”列为控制措施。
9)探测度
探测度是指在失效发生后,基于当前的控制措施多大程度能防止缺陷流出。不要想当然地认为发生度低,探测度就高。随机抽样难以检查出单例的孤立缺陷,因此可认为其随机抽样是无效的探测措施,而基于统计学的合理抽样是有效的探测措施。
探测度是一个相对概念,不是绝对的;当没有采取探测措施时,如果采取了防错(Error-proofing)措施,则探测度D=1,否则探测度D=10。
探测度是根据探测措施类型来评价的,即探测措施类型决定探测的有效性,如下表。
10)风险等级
RPN=S*O*D,RPN不是识别采取优先措施的唯一指标,因此不要设置RPN阀值,说“RPN超过某个值就要采取行动,低于某个值就不需要采取行动”。
11)建议措施
制定建议措施的目的是降低风险,优先考虑用预防性措施来降低发生度;建议措施关注的顺序:1)高严重度(S=9/10,O≠1);2)高危害度(S=5-8, O=4-10);3)高RPN。任何严重度达到9/10等级的失效模式,必要要评估通过设计变更或过程变更来降低严重度/发生度的可行性。经评估后无需采取建议措施时,在建议措施栏写“无”;若未确定是否采取建议措施,则建议措施栏暂时留“空白”。
参考资料:
SAE J1739, 2009-Potential Failure Mode and Effects Analysis in Design (Design FMEA), Potential Failure Mode and Effects Analysis in Manufacturing and Assembly Processes (Process FMEA)
文章转自:质量管理笔记