共计 7221 个字符,预计需要花费 19 分钟才能阅读完成。
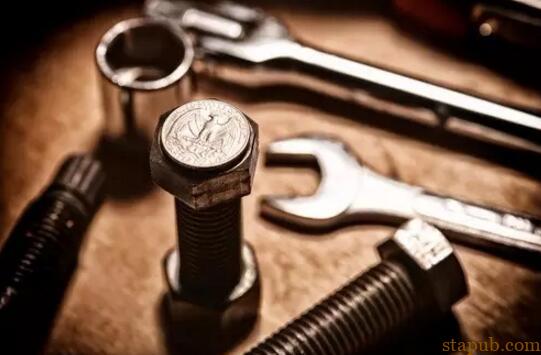
紧固件通过扭矩法安装,直观、简便、易于操作;通过摩擦系数来确定安装扭矩,数值精确,安装的可靠性比较强。
一、扭矩系数、摩擦系数之间的关系及计算公式:
1. 螺栓副的扭矩系数:
扭矩法易于理解,在弹性范围内,扭矩值与预紧力一般呈线性关系,扭矩值随着预紧力的增加而加大;因此扭矩法,可以在测量扭矩系数后,具体的数值可以根据螺栓的规格,查找GB/T3098.1相应的标准,可以得出具体的扭矩数值,操作简便。具体参见下面的公式:
T=K?F?D
T—扭矩
K—扭矩系数
F—预紧力
D—螺纹的公称直径
扭矩系数是紧固件连接副安装时,必须要了解掌握的一个重要技术参数,目前安装扭矩、扭矩系数已经受到广大使用者的广泛理解、接受,并且在安装时普遍受关注。扭矩及扭矩系数是既有联系又有区别的两个参数。
当扭矩数值选定后,扭矩系数越小,产生的紧固力越大;扭矩系数越大,产生的紧固力越小。当扭矩系数小到一定的程度,在一定的扭矩的作用下紧固力超过了螺栓的强度极限,高强度螺栓就会产生伸长甚至断头的现象;反之,扭矩系数过大,产生的紧固力就会过小,整个螺栓连接副就达不到锁紧的功能,连接副就有可能产生松动情况。
因此,要使紧固力在一个标准的范围内,产品的扭矩系数就要限定在一个规定的范围内。
目前国家紧固件标准GB/T 1231-2000对钢结构用高强度螺栓连接副的标准作了规定,扭矩系数K=0.11-0.15,标准偏差≤0.010。使用单位一般比较重视扭矩系数,认为扭矩系数确定后,马上可以确定安装扭矩,进而可以实施紧固件连接副的安装;但是对标准偏差则容易忽视。如果标准偏差>0.010,在安装时,就会产生个别螺栓的预紧力偏离比的现象:标准偏差值偏大或者偏小,都会造成个别紧固件连接副过拧或者拧不紧的现象,对安装可靠性存在隐患。
如果扭矩系数偏大,标准偏差在<0.010的范围内,连接副离散度非常小,每一副紧固件的受力比较均匀;扭矩系数偏大,会在安装时增加一些扭矩数值,但是不会产生过拧或者松动的现象,安装的可靠性、安全性增加。因此,从某种角度来讲,标准偏差比扭矩系数更加重要。
2. 螺栓副的摩擦系数:
在螺栓安装时,摩擦总系数,包含螺纹扭转摩擦与端面摩擦现象,可以通过摩擦系数试验机来进行各项摩擦系数的测定,因此,可以将安装扭矩分为三个部分:螺母与垫圈平面之间的支承面摩擦,占安装扭矩的50%左右;螺栓螺纹与螺母螺纹间的摩擦,称为螺纹摩擦,占安装扭矩的40%左右;真正转化为紧固轴力的称为预紧力,只占安装扭矩的10%左右;由此可见,在紧固件连接副安装时,大部分的安装扭矩都在前两个摩擦中损耗。。
上海的几家高强度紧固件公司做了大量的摩擦系数相关实验,与理论叙述的概念一致,大部分的安装扭矩都在前两个摩擦中损耗,但是实际数值略有不同;三部分的扭矩数值的分配为:螺纹间的摩擦损耗安装扭矩30%~40%;支承面之间摩擦损耗安装扭矩40%~50%;真正转化为夹紧力的扭矩一般在10%~20%左右;而且粗牙螺纹与细牙螺纹也存在一定差别。下面的图表一是一家外资检测公司经过一系列摩擦系数的实验得到的实验数据,可以反映了螺纹摩擦扭矩、支承面摩擦扭矩与夹紧力间的相互关系。
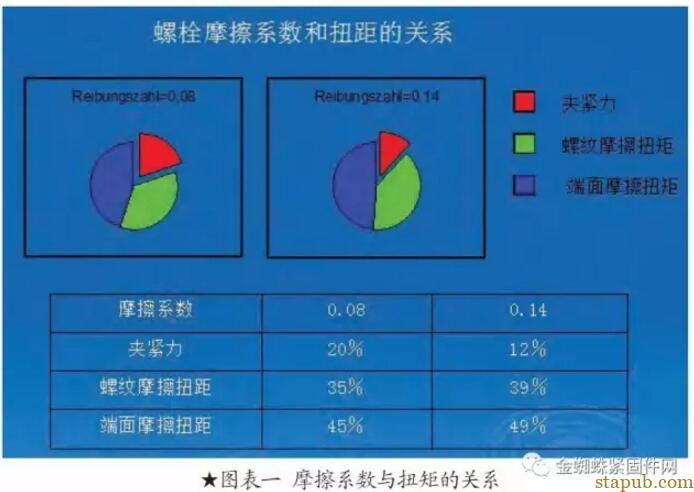
摩擦系数对夹紧力影响很大,摩擦系数越小,对夹紧力数值的贡献越大;反之,摩擦系数越大,对夹紧力数值的贡献越小。
在正常提供合格的摩擦系数要求范围内,预紧力占总扭矩的10%是理论阐述分析的数值,不是实际的安装扭矩的预紧力分配的数值;如果高强度紧固件表面状况改善,摩擦系数系数会下降,夹紧力的数值也会相应地提高,能够有效地增加预紧力扭矩的数值,安装连接的紧固度也可以增加。
在一般正常的情况下,端面摩擦大于螺纹摩擦。
3.摩擦系数的计算公式:
总摩擦系数与支承面摩擦系数、螺纹摩擦系数有数学公式关系,可以进行具体的计算:
摩擦系数的计算公式:
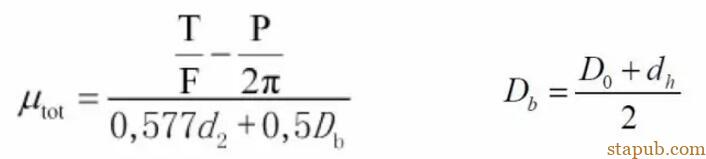
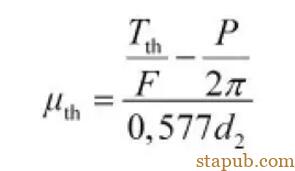
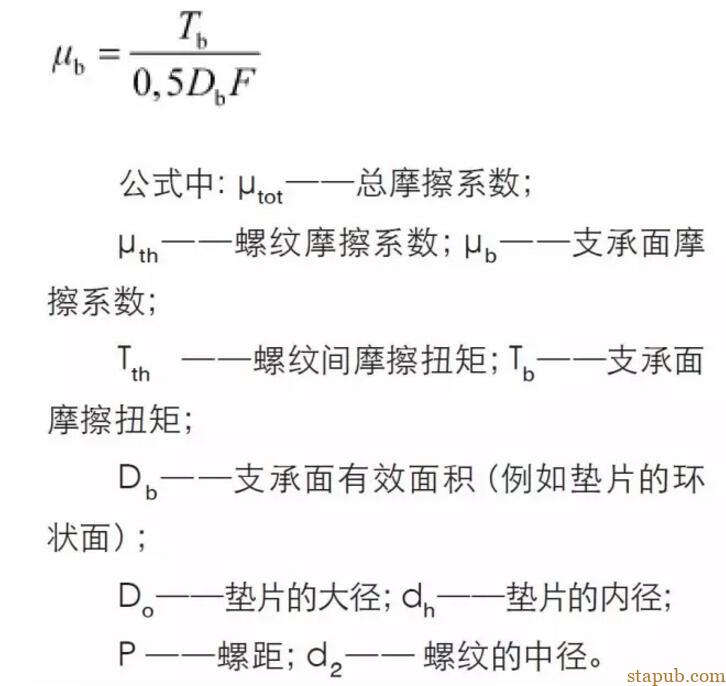
国家标准GB/T16823.3 -1997《螺纹紧固件拧紧试验方法》,国际标准ISO16047—2 0 0 5《紧固扭矩— 轴向预紧力试验》有些区别;G B/ T16 8 2 3 . 3国家标准与日本标准JIS1083-1990《螺纹紧固件通则》等效,ISO16047—2005叙述更加深入详细,标准里面的字母代表各不相同;
扭矩系数与支承面摩擦系数、螺纹摩擦系数的关系不能用确切的数学公式来表示,但是他们之间的关系可以采用表格的形式来反映,表明了一定的对应关系:
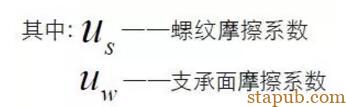
扭矩系数偏大,在安装时施加扭矩要大幅度地增加。扭矩过大,超过屈服点,会造成超拧,拉长,甚至断裂的情况;当安装扭矩确定后,如果扭矩系数偏大,分配到紧固轴力数值会偏小。钢结构安装时规定的扭矩系数为0.11~0.15,目前一般制造厂在润滑状态下均能控制在这个区域,关键是如何控制好离散度,使标准偏差在0.01以下,偏差数值越小,说明紧固件的一致性越好,对安装可靠性、安全性也越有保障。
安装扭矩与支承面摩擦系数、螺纹摩擦系数的计算:
通过摩擦试验机,可以测量出的摩擦系数的数值,这样能够了解紧固件在部件安装时每个摩擦系数的状况及各系数之间的关系;同时通过下列公式,计算出摩擦系数对安装扭矩的影响,扩大了安装扭矩的计算途径,打破了许多公司认为只有通过扭矩系数K才能计算安装扭矩的观念,详见表三:
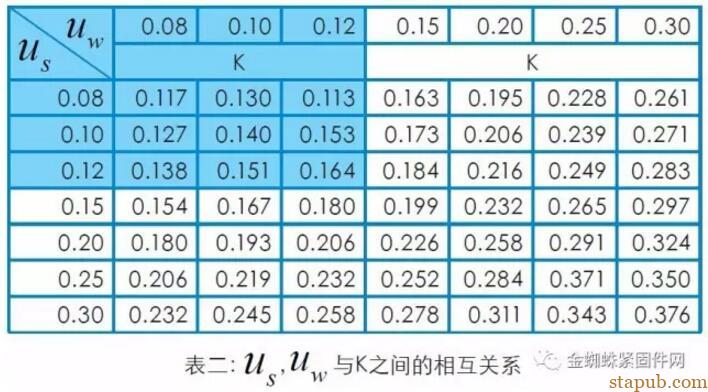
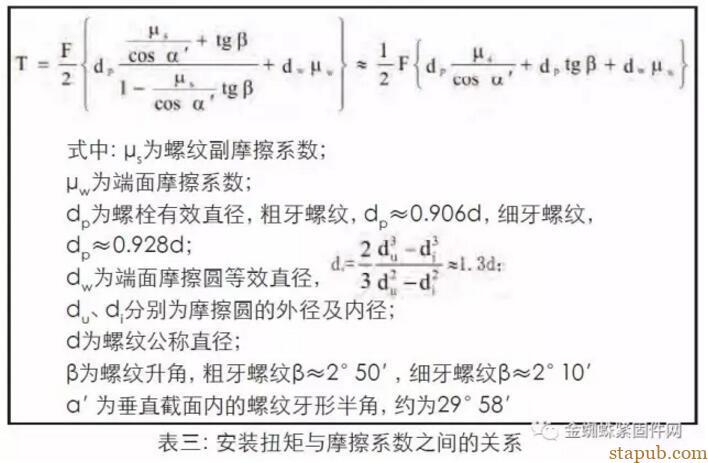
1、产品表面状况对扭矩系数、摩擦系数的影响:
表面状况对扭矩系数K的数值影响很大,它直接关系到安装扭矩及紧固轴力数值。高强度紧固件连接副不同的表面状况,对扭矩系数、摩擦系数产生很大的影响。在一般情况下,产品表面粗糙、加工痕迹明显对高强度紧固件连接副扭矩系数、摩擦系数数值会增加,进行润滑后,扭矩系数、摩擦系数可大幅度地下降,这对紧固件安装的可靠性、扭矩系数与摩擦系数一致性影响很大。
润滑后扭矩系数、摩擦系数下降幅度一般在20%~50%左右,有些比较好的润滑方式,扭矩系数K可以下降80%甚至100%以上,我们对高强度紧固件连接副各种表面状态进行了一系列的试验,得出各种表面状况对扭矩系数K的影响状况,具体见表四。
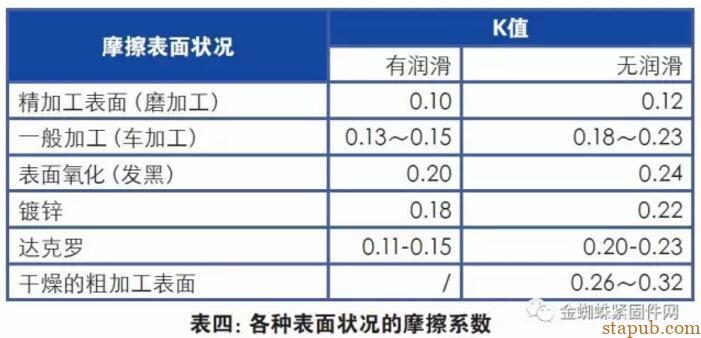
润滑剂能有效地降低摩擦系数、扭矩系数,其积极作用显而易见,但是不同类型的润滑剂产生的作用区别很大:
不同润滑剂对扭矩系数的影响:
我们公司M30的螺栓连接副,经过Delta-Mks表面处理,盐雾试验达到720小时,表面处理后,我们测得扭矩系数在0.20~0.24范围内。
但是,用润滑剂后,扭矩系数直线下降;而且不同类型的润滑剂,扭矩系数下降的幅度不同。我们采用两种不同的润滑剂进行螺纹表面润滑:一种是Molykote 1000的油脂性润滑剂;另外一种润滑剂是上海达克罗公司25%的白色油性润滑剂,分别用了五套连接副做试验,情况见表五。
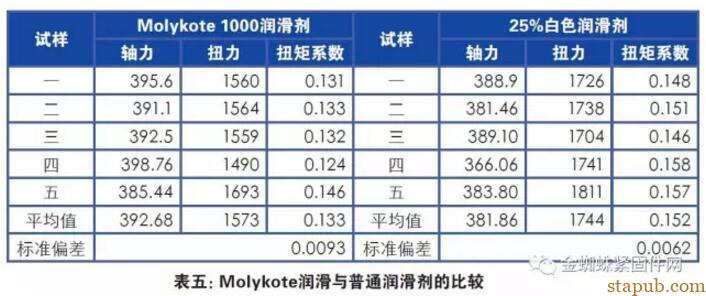
相同润滑种类,不同工艺对扭矩系数的影响:
以表面磷化为例,同样的表面磷化处理,不同参数对扭矩系数影响大,表面磷化处理能在产品表面产生细小致密的微孔,由于微孔直径细小均匀,有吸附及存储液体的作用,能有效防止粘连、咬合的作用;而且,由于磷化表面层均匀性、一致性良好,它对扭矩系数的均匀性也同样起到良好的作用,因此是汽车行业常用的表面处理方式。
但同样的磷化处理,除了牌号不同外,不同的工艺方法对扭矩系数也会带来一定的影响。磷化表面层对汽车紧固件扭矩系数的影响,经过反复的试验与论证,可以得到以下结论:
1)在未经任何封闭的条件下,磷化温度高,其摩擦系数低。
2)磷化工艺及磷化种类对封闭后的摩擦系数影响不大,影响摩擦系
数的关键因素是封闭剂。
3)磷化封闭后,烘干温度高,其摩擦系数略有提高,尤其是螺纹部分的摩擦系数提高较多。封闭处理时,应该充分考虑紧固件摩擦系数的要求范围,摩擦系数甚至可以通过封闭剂种类及黏度来较为准确地调控摩擦系数。
同一种润滑剂,不同涂装部位对安装扭矩的影响:
如今润滑越来越被人们重视。不仅润滑剂的种类不同、润滑工艺的不
同会给安装扭矩产生不同的影响,就是同一种润滑剂,由于涂装部位不同,扭矩系数也会带来很大的变化。润滑方位越是全面,扭矩系数会越小。
我们公司对M36大六角螺栓,用同样Mol ykote1000的润滑剂,由于涂装部位不同,产生的K系数值也不同:
一组是在螺栓与螺母上涂润滑剂,8套螺栓连接副的扭矩系数平均值0.126,标准偏差0.0058,具体见表六。
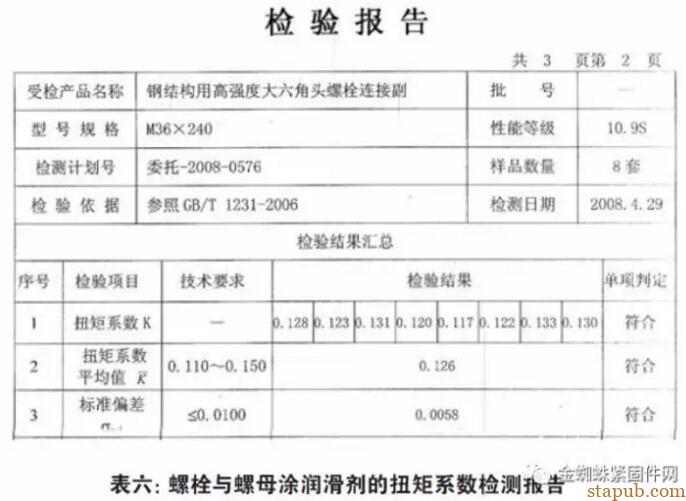
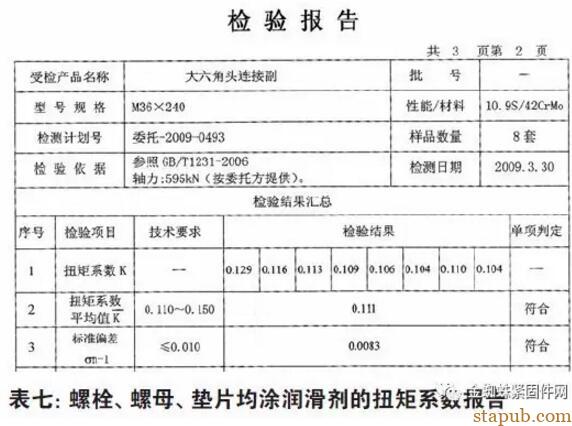
上海某高强度紧固件有限公司,经过多次试验及测量,在垫圈平面加Molykote后,扭矩系数直线下降。一般螺纹涂润滑剂扭矩系数在0.120~0.125之间,而增涂垫圈面后扭矩系数在0.090~0.010之间,下降25%左右,个别批次的扭矩系数最低可达到0.087,因而全面润滑对扭矩系数下降作用很大,值得安装使用单位深思,这一数值也符合扭矩系数的分配规律。
螺母的润滑状态比螺栓更重要:
经过多次实验,我们可得出实践结果:螺母均匀地润滑对扭矩系数的下降起很大的作用,比螺栓的润滑更为重要。
例如,对M20*100的大六角螺栓连接副的扭矩系数几次测定数值状况:
在M20*100的大六角螺栓连接副的扭矩系数测定中,我们在垫圈平面螺栓螺纹处均匀地涂上Molykote1000的二硫化钼润滑脂,螺母内圈比较难涂,只能象征性地蜻蜓点水抹了一些,结果测出扭矩系数偏大,为0.137,具体见表八。
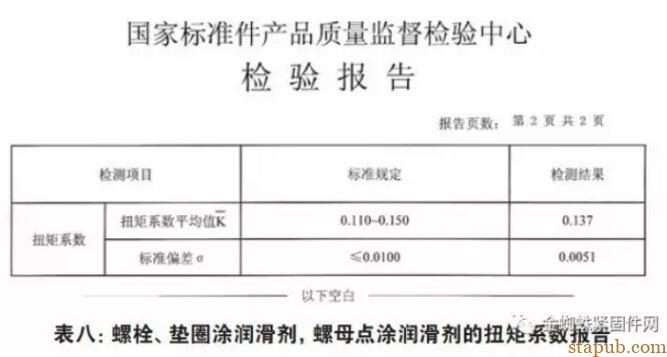
为了达到客户规范的要求,我们又重新拿了八组螺栓连接副,对螺栓、螺母、垫片、重新认真涂抹,尤其是螺母内螺纹做到每牙都均匀地抹上Molykote1000润滑脂,紧固件研究所测定,扭矩系数大幅度下降,达到0.119,符合客户企业标准,具体见表九。
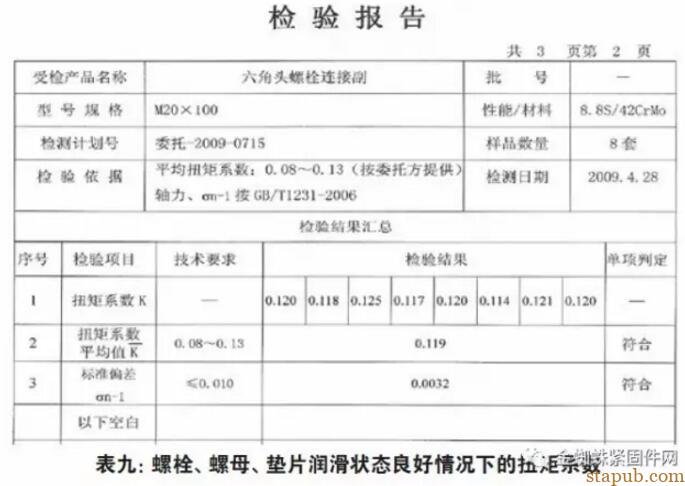
三、摩擦系数对螺栓副安装产生的影响:
实例说明——福建某风场螺栓安装跟转实例分析:
在福建莆田沿海某风场,在风机紧固件连接副安装时,有四个紧固件制造公司进行供货:两家公司安装情况正常;但是另外两家公司的紧固件连接副,在安装时,出现20%—25%左右的螺母在旋合时发生跟转——即螺母在扳拧时,六角螺母与在六角螺栓头部同一方向旋转,形成打滑、拧不紧的现象,如图一B,给现场施工带来不便,影响正常安装。
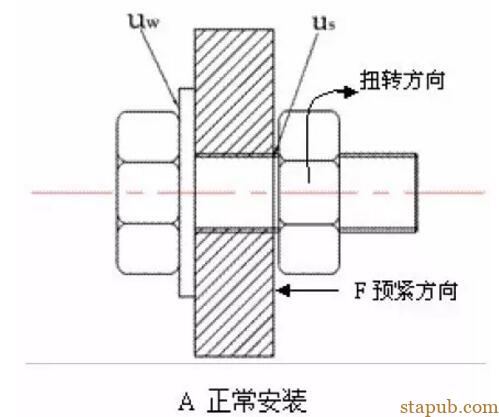
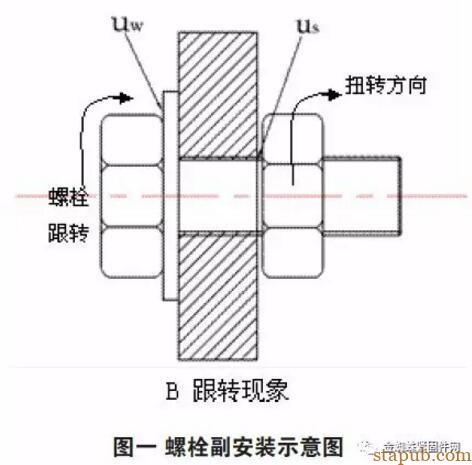
1、跟转产生的原因:
摩擦力的分配关系:
国家标准GB/T 16923.3——1997《螺纹紧固件拧紧试验方法》明确叙述:安装扭矩分为三个部分:螺栓与螺母间的扭转摩擦,螺纹间产生的摩擦力矩要占总安装扭矩40%左右;螺母与垫圈平面之间的平面摩擦,螺母与垫圈平面之间力矩要占总安装扭矩50%左右。在安装时,大部分安装扭矩都在前两个摩擦中损耗,直接转化为预紧力的只占紧固扭矩的10%左右。如果螺纹间产生的扭转摩擦力增加,数值超过了螺栓与垫圈平面之间的支承面摩擦力,那么,螺栓就会产生与螺母一起转动的现象——习惯上称为跟转。
产生跟转的原因:
跟转一般产生在螺纹间隙公差控制在比较小、润滑不到位的情况。如果螺纹公差控制比较严格,螺栓连接副在使用中安全,不容易产生滑丝、脱扣现象。如果放大螺母中径,配合比较松,螺纹间隙增加,螺纹间的摩擦力自然会减少,安装时比较省力,也会消除跟转的现象;但是,在使用中会增加脱扣的风险,重视紧固件螺纹配合质量的高强度紧固件制造公司,公差控制比较严格,如果碰上表面处理厚度略微增大,螺纹间的间隙减少了,很容易造成安装出现跟转的现象。经过分析,产生跟转的情况有四种可能性:
螺栓副螺纹配合比较紧密,配合间隙比较小;
螺栓副螺纹制造比较粗糙,在旋合时摩擦阻力大;
垫圈平面光滑,形成摩擦阻力小,这样螺纹之间摩擦力相应地增加;安装时润滑不到位。
在以上四个方面,会出现四项中几项兼有的状况,其中,螺纹制造公差及安装时润滑不到位,是产生跟转的主要原因。而且润滑重要性往往不被人们所重视,不仅润滑剂的种类不同、润滑工艺的不同,会给安装扭矩产生不同的影响;即使是同一种润滑剂,由于涂装部位不同,扭矩系数也会带来很大的变化;润滑方位越是全面,扭矩系数会越小。
如果排除螺纹制造公差的问题,消除跟转的最积极有效的途径是增加润滑,合理地调配润滑,减少螺纹间的摩擦力。
螺纹间润滑增加后,螺纹摩擦力减少了,扭转摩擦下降了,螺母与垫圈平面之间的平面摩擦相应地按比例增加,当平面摩擦 >扭转摩擦 ,跟转情况有效地消除了。
垫圈平面光滑,形成摩擦阻力小,也容易造成螺栓跟转拧不紧的现象。
山东一家公司采用垫片喷丸打毛的方法,增加端面摩擦,收到了一定的效果,在安装时,螺栓的跟转比例,从起初旋合时20—25%下降到5—8%,但是还是存在个别紧固件跟转的现象,没有彻底地解决安装时的螺栓的跟转问题。
2、原因分析:
经过现场安装情况的仔细查看分析,发现福建莆田沿海风场跟转的现象是由于润滑不到位所造成的。现场安装实行计件制,安装工程队为了安装进度和经济效益,涂润滑油脂比较粗糙。由于在螺栓、垫片外表面涂润滑油脂,比较容易涂抹,但是螺母内孔比较难以涂抹,只是象征性地涂抹一下,润滑状态没有达到要求,使得螺纹之间的摩擦大幅度地增加,当螺纹间的摩擦超过了支承面间的摩擦,就会导致跟转,即拧不紧的现象。
找出来原因后,我自己用刷子对六角螺栓、六角螺母垫、垫片按照技术规范进行润滑脂涂抹,一共涂抹了十套,现场进行安装;十套紧固件连接副全部顺利完成安装连接,没有发生跟转——拧不紧的现象。
3、解决方案:
现场完成紧固件连接副装配后,马上用书面文件填写安装润滑的工艺文件:
根据我们公司提供的扭矩系数、安装扭矩进行安装。
润滑的技术条件与方式:
①用MolyKote1000的。
②垫圈与螺母接触平面、螺栓、螺母都必须均匀地涂抹,尤其螺母螺纹间的涂抹均匀度是关键所在,必须认真涂抹,螺母的全部螺纹必须涂抹均匀。
如何预防安装现场风吹产生的灰尘沾在紧固件上?由于灰尘粒子会增加摩擦力,必须采取一边涂抹一边安装方法,或采取确实有效的防尘措施。
经过现场察看、技术指导,福建莆田沿海风场编排了具体地安装润滑的技术工艺要求,有效地解决了紧固件连接副的跟转情况,顺利地完成了30台风力发电机安装、并网、发电的任务。
紧固件安装看似简单,实际上技术含量比较高。随着技术进步,人们对紧固件质量意识的观念不断提高,从原来单一制造的观念逐步到材质—制造—热处理—表面处理—安装的全面产业链,是紧固件生产使用全方位的、缺一不可的、延伸制造、技术服务的理念。
尤其重要的是,要全面地了解扭矩系数、摩擦系数、安装扭矩等几个方面重要的技术参数及其内在含义,尤其是扭矩系数、摩擦系数,两者既有联系又有区别,他们有各自不同的技术层面、不同的特点、不同的参数、不同的测试方法、不同的应用领域,但都是反映高强度紧固件安装中具体的扭矩数值,都是为了确保高强度紧固件连接副安装的可靠安全。
因此紧固件制造企业必须提高思想理念、延伸制造领域、开拓售后技术服务,提高紧固件产品的技术含量,不断地开拓创新,使紧固件企业立于不败之地。
本文作者:金蜘蛛紧固件网顾问专家 阎振中
本文原载于金蜘蛛《紧固件》季刊杂志第35和36期,转载请注明作者和来源。