共计 3663 个字符,预计需要花费 10 分钟才能阅读完成。
螺栓拧紧扭矩可以分为动态扭矩和静态扭矩,他们对于产品最后装配的效果影响很大。所以,在实际加工过程中,区分这两者就显得至关重要。
一般工具或设备先预设的扭矩值也就是动态扭矩值,预先设定的扭矩值往往是图纸中规定的扭矩值的公称值,例如,图纸规定一个螺栓连接的拧紧扭矩为100Nm±10Nm,在工具设置扭矩时候应设置100Nm的公称拧紧扭矩,后面是扭矩的公差。
虽然现在的拧紧工具精度都非常高,电动拧紧枪的精度可以达到±3%以内,甚至这些拧紧枪的精度都是3σ的精度,那么,为什么在图纸设计中扭矩公差一般还是用±15%,或±10%呢?一般情况下,如果设计扭矩公差更低,例如±5%,工艺部门一般很难同意,这是什么原因呢?
拧紧工艺验收时候,一般要求Cm≥2,Cmk≥1.67,如果设计的扭矩公差为±5%的情况下,试想一下,这个拧紧工艺最后验收的时候,能否达到CCm≥2,Cmk≥1.67的要求?在长期能力指数(工序能力指数)还要求Cpk≥1.33。
所以,从这个意义上来说,要满足Cm≥2的要求,扭矩公差至少要保证比拧紧工具的精度放大2倍。也就是说现在一般拧紧工具精度可以达到±3%的情况下,至少扭矩公差要设置在±6%以上,否则,就可能Cm无法到2的要求。为了保险起见,因为Cm≥2是一个最低要求,因此,扭矩公差应再放大一些,例如拧紧工具精度的3倍,这样是不是就可以比较容易的达到设备能力指数的要求了呢?
至于设备能力指数Cmk≥1.67,这个是完全可以通过拧紧工具标定小车,校准小车来进行校准,尽量把中间值落在拧紧扭矩的公称值附近,非常接近公称值,这个通过拧紧工具的校准是可以达到的。
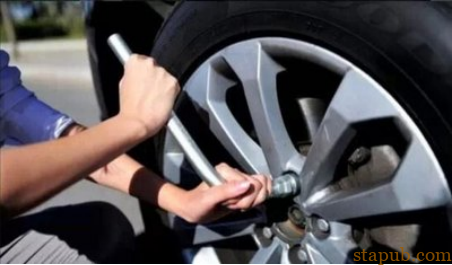
就是指一个紧固件已经被紧固好之后,我们用扭矩扳手(一般是扭矩扳手,当然也可以在实验室用电动拧紧工具测量静态扭矩。
车间中大部分是用扭矩扳手,不同企业要求不一样,这种扳手包含表盘式扳手、数显式扳手、带角度的数显式扳手、通过特殊的软件功能直接读取最低值的静态扭矩扳手等)继续沿着拧紧的方向旋转,所测得的扭矩值。这个时候如果是用表盘式扳手、普通数显扭矩扳手往往测量的是最大值。而用专用测量静态扭矩的扭矩扳手,可以根据软件设置的不同类型,显示出静态扭矩值。
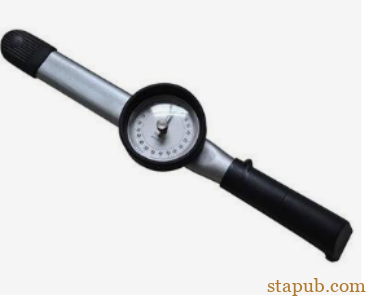
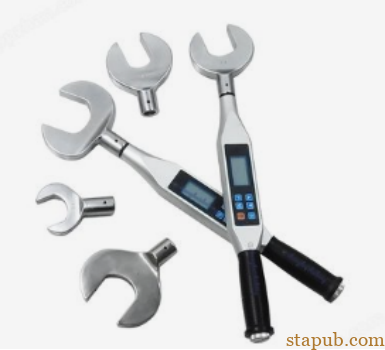
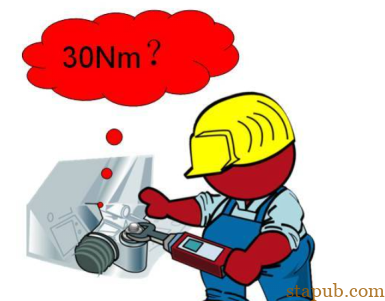
例如:VDI 2230标准要求静态扭矩范围是动态扭矩公称值的0.85-1.3这个范围。大众要求为0.8-1.2(对于C级件,允许达到0.7-1.2,对于自攻钉,被连接件有塑料件等容易衰减的软连接类型允许范围为0.5-1.2)。
上次在某一个会议上,有位小伙伴对这个方面进行了总结,附照片,供大家参考。
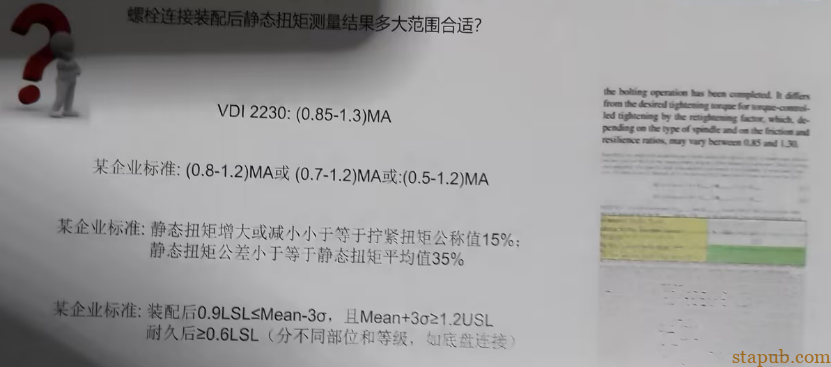
MNA1 ≥ 0.80 × MA 且 ≤ 1.2 × MA
MNA1 ≥ 0.70 × MA 且 ≤ 1.2 × MA
非公制螺纹(如自攻钉ST螺纹、PT螺纹)
一个或多个夹紧的塑料件、橡胶件(软连接类型)
其静态扭矩极限值为:
MNA1 ≥ 0.50 × MA 且 ≤ 1.2 × MA
所以,螺丝君比较赞同大众这个标准,后续我们进行详细的说明和分析具体原因。
按照现在能够测量静态扭矩专用扳手的测量结果,在测量操作等都比较可靠的前提下,基本可以认为静态扭矩的发生了衰减,螺栓的轴力也会发生衰减,而且衰减比例也是大致等比例关系。
正是由于上述静态扭矩与轴力存在着相对正比例的关系,后续我们可以对这个静态扭矩的合理范围给出分析。
如果是比较薄的被连接件,由于螺栓夹紧长度短,螺栓和被连接件的柔度都比较小,从而同样的接触面数量,同样的嵌入损失情况下,螺栓连接的轴力嵌入损失更大。
后续,在分析一些BC类连接时候就可以允许更大轴力衰减,也就是说有允许更大的静态扭矩衰减,因为这些衰减在嵌入损失计算中都已经考虑了。当然,即使这个时候轴力衰减能够满足外载荷要求,因为夹紧长度短,轴力损失比较大,还是要对承受载荷比较大的这种连接点位置额外增加一定的防松措施。
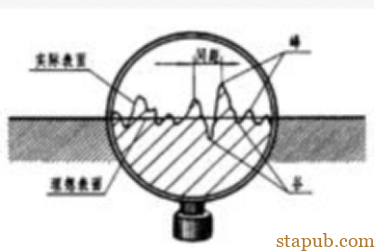
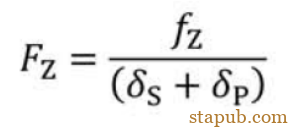
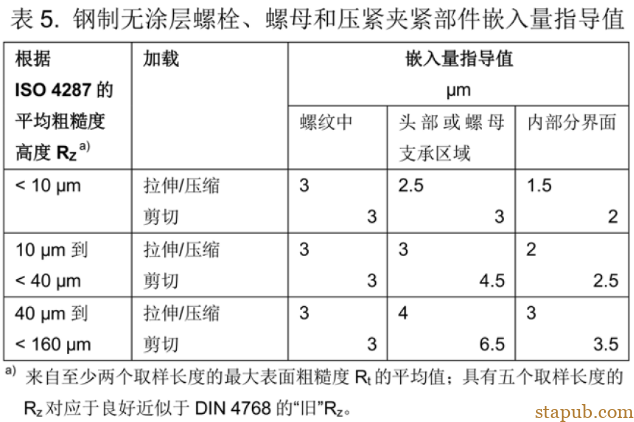
螺栓连接装配后,由于多层板冲压或焊接的不平,同时多层板之间还会存在着间隙,这样螺栓装配以后,在螺栓较大预紧力作用下,零件就会产生塑性变形,造成预紧力的损失。
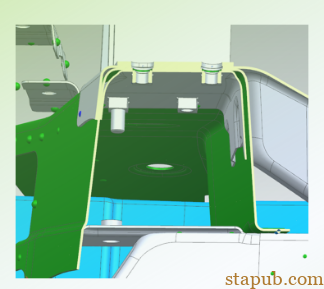
从这个意义上说,由于被连接件的一些设计、质量原因导致的扭矩衰减往往更加不能忽视。或者说这样的零件,扭矩衰减是不可避免的。那能够允许出现多大的衰减呢?
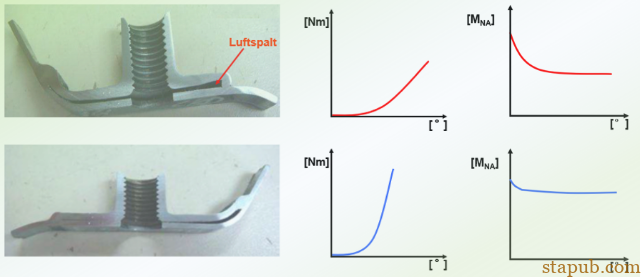
这个扭矩公差为什么是±15%?一方面是因为前面说的拧紧工具的验收要求满足设备能力指数,另一方面,我们认为就是这个扭矩衰减的问题,在计算时候按照减小15%计算出来的预紧力是要必须满足外部载荷的要求的,也就是说在按照公称扭矩减少15%,这个螺栓连接在设计计算中仍然是满足要求的。同时,在计算中又考虑了约为5%的嵌入损失造成的预紧力下降。故总体认为预紧力下降20%在理论上能够满足设计所需的预紧力的要求的。
从这个分析来看,大众标准要求的对于AB类螺栓连接,允许衰减20%是合理的,而且即使衰减了20%,螺栓的预紧力仍然是能够满足载荷要求的。
对于C类螺栓连接大众标准允许衰减30%,这主要是因为C类螺栓连接本身所受载荷不大,相对来说设计余量更多一些,故可以运行更大的扭矩衰减。这个就是前面嵌入损失计算中,C类螺栓往往像车身连接部位,存在很小的夹紧长度,同时,往往载荷也会比较小,所以,也就是可以允许更大的嵌入损失,更大的静态扭矩衰减。
对于有塑料件,非米制螺纹的BC类螺栓连接,大众允许衰减50%,一方面是因为这些部位本身就是软连接部位,很容易出现因为蠕变,松弛导致的预紧力衰减,同时,这些部位相对要求会比较低一些。如果要求比较高的螺栓连接部位,即使是塑料件的连接,在设计时候一般都会考虑增加衬套的方法来降低扭矩衰减,因为此时这些部位非常关键,是关键的螺栓连接点,相应的扭矩衰减要求也会更高。例如制动踏板部位采用的塑料件连接零件,但是,该部位的要求还是非常重要,故在塑料件螺栓连接部位要嵌入一个金属衬套,来达到降低扭矩衰减的目的。
从这个意义上来说,如果是AB类的螺栓连接扭矩衰减也不能太大,即使零件是存在较大衰减可能的塑料件软连接类型,必须从设计上来改变这种扭矩衰减太大的可能。
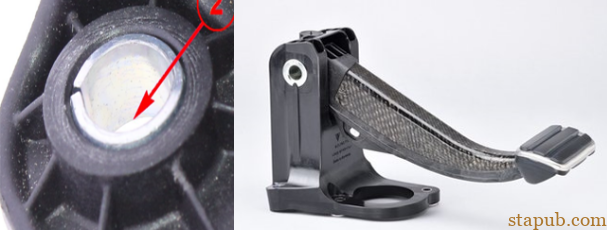
从这个意义上,扭矩公差这些大公司,例如大众、通用、福特等公司都是一般默认为15%的公差不仅仅是对拧紧工具精度的要求,设备能力指数Cmk的要求,同时,也是对扭矩衰减起到关键的作用,说明在设计时候已经考虑了 这么大的衰减仍然是能够满足载荷要求的。
对于塑料件等连接部位,允许更大的衰减,主要是因为这些部位的载荷相对比较小,即使产生比较大的衰减,仍然能够满足载荷的要求。另一方面这些带塑料件等连接部位,常温下就会因为塑料件的蠕变,松弛产生很大的衰减不可避免。
如果在塑料连接部位,载荷比较大,要求比较高,就要从设计上改变这种塑料件夹在被连接件中的连接形式,例如通过衬套来支撑在塑料件中减少扭矩衰减。
文章来源:网络